No end in sight for industrial property boom as companies bring manufacturing onshore
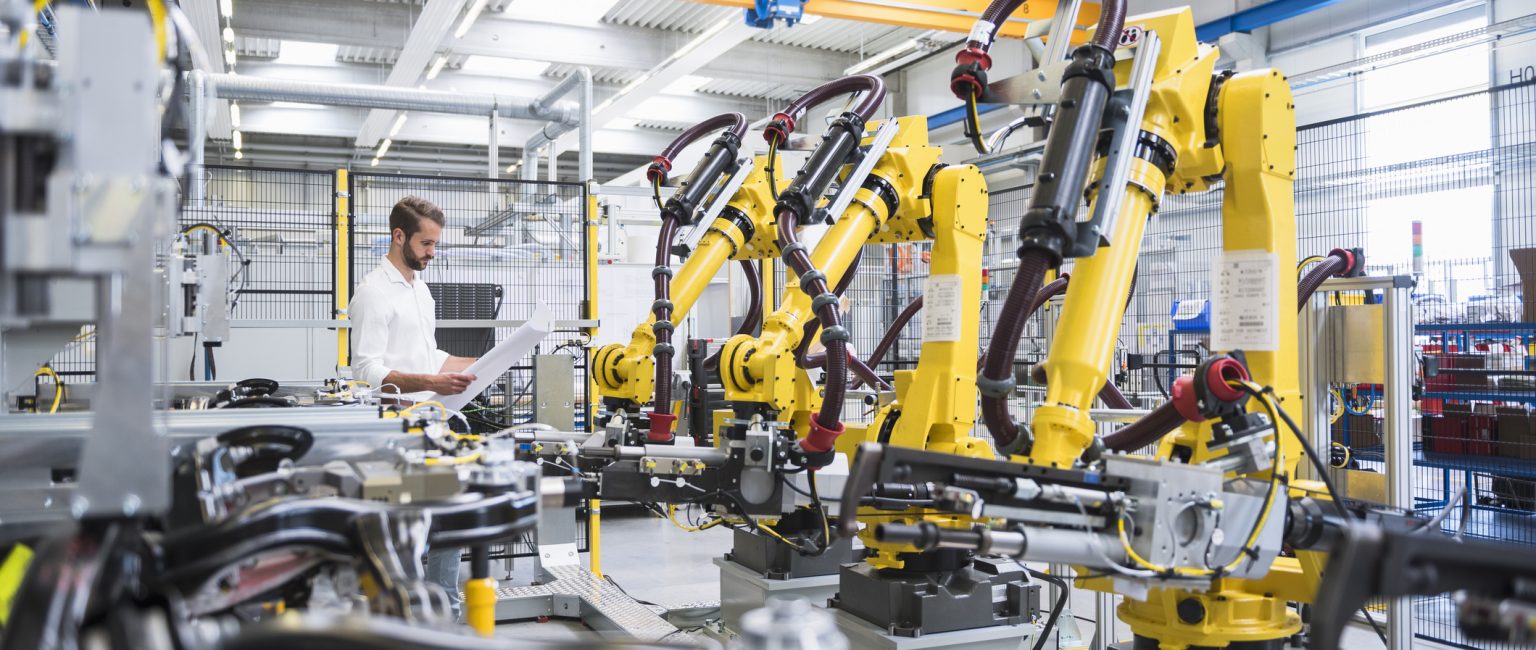
Advances in technology and automation can make manufacturing onshore cost-effective and efficient, which means the high demand for industrial real estate is going nowhere.
Disrupted supply chains and escalating shipping costs unleashed by a global pandemic and ensuing geopolitical unrest has prompted an increasing number of Australian companies to bring their manufacturing back home, or to at least consider it.
The trend, which could further drive demand for industrial real estate, marks a significant shift from the 1990s and 2000s when the allure of offshoring gripped Australian businesses. Back then, the combination of high local labour costs, a dwindling pool of unskilled workers, and the expansion of international supply chains drove many to relocate production to Asia.
Now, the pendulum is swinging back the other way.
A 2023 KPMG report found 84% of Australian companies are ‘nearshoring’ or ‘onshoring’ operations or considering it, while Prological’s Supply Chain Pulse Check this year showed 28% of businesses are considering reshoring and 17% maybe considering.
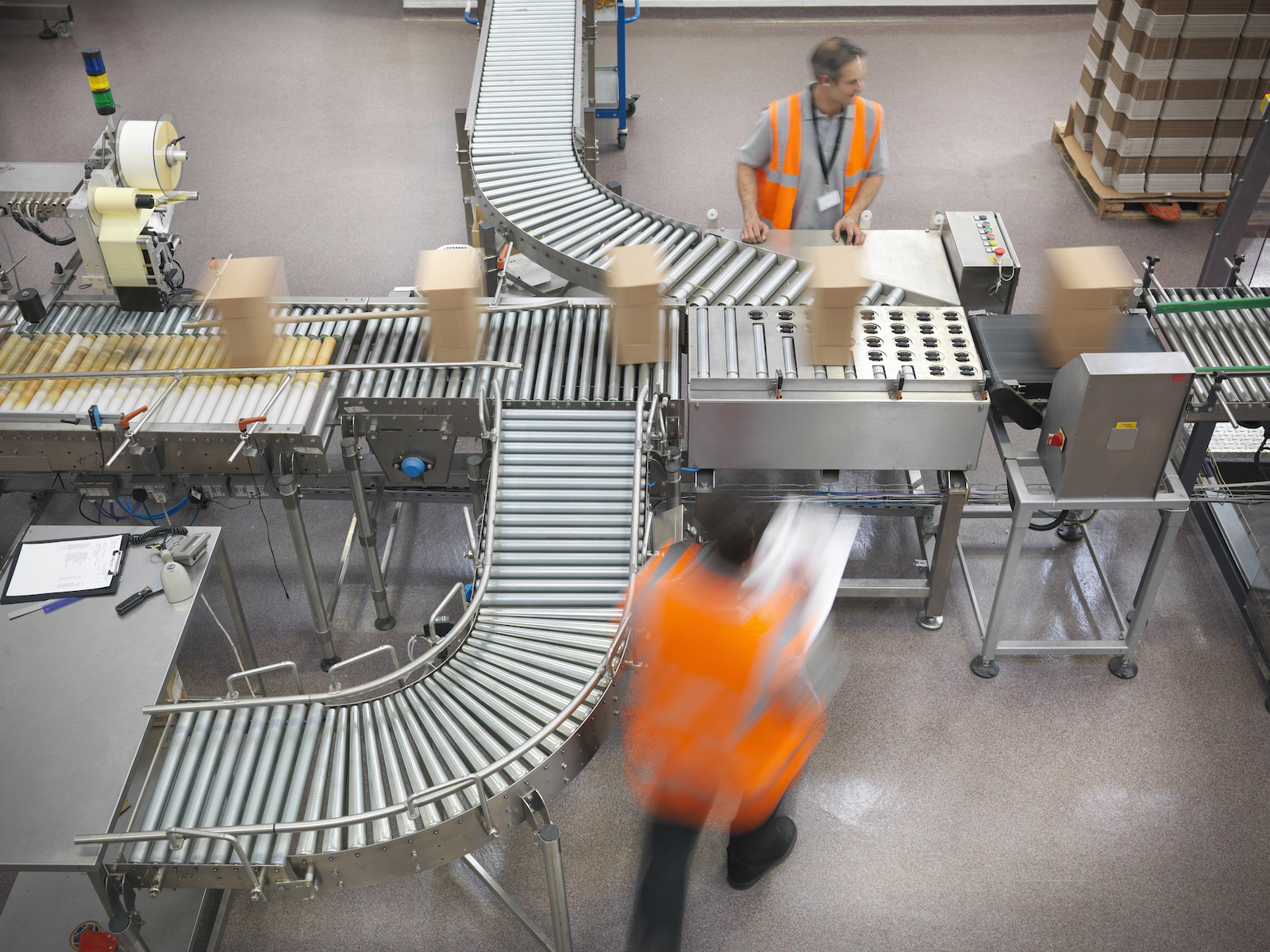
Supply chain disruptions are prompting Australian companies to consider bringing manufacturing back onshore. Picture: Getty
PropTrack economist Anne Flaherty says this trend has already bolstered the industrial real estate sector.
“Industrial rents grew at the fastest rate on record over 2022 and are still rising in 2023, while vacancy is at record low levels as growing occupier demand outpaces the speed at which new industrial is being developed,” Ms Flaherty said.
At the same time, the online shopping boom continues to propel consumer demand. E-commerce revenue is projected to hit $58.54 billion in 2023 and grow by 9.78% per year to reach $85.03 billion by 2027, according to Statistica.
‘Just-in-case’ approach boosts warehouse storage demand
Ms Flaherty says a key factor driving the need for more warehouse space has been the transition by many businesses away from a ‘just-in-time’ to a ‘just-in-case’ approach to managing their supply chains.
“Prior to 2020, just-in-time was generally the most practical, cost-efficient way of managing supply chains. In the three years since, however, supply chain engineers have seen their strategies upended by a global pandemic, a war in Europe, escalating geopolitical trade tensions, and adverse weather events. Not to mention material and labour shortages,” she said.
“These challenges are leading more businesses to adopt a just-in-case approach and increasing inventories to ensure goods can still be manufactured and delivered in the event of unexpected shortages or delays.”
However, the approach is more expensive, less efficient and necessitates businesses to ‘stock up’, she said, which requires more warehouse space to store goods
“But when the alternative is empty shelves and an inability to deliver to consumers, more businesses are finding they have no choice but to adopt this approach,” she said.
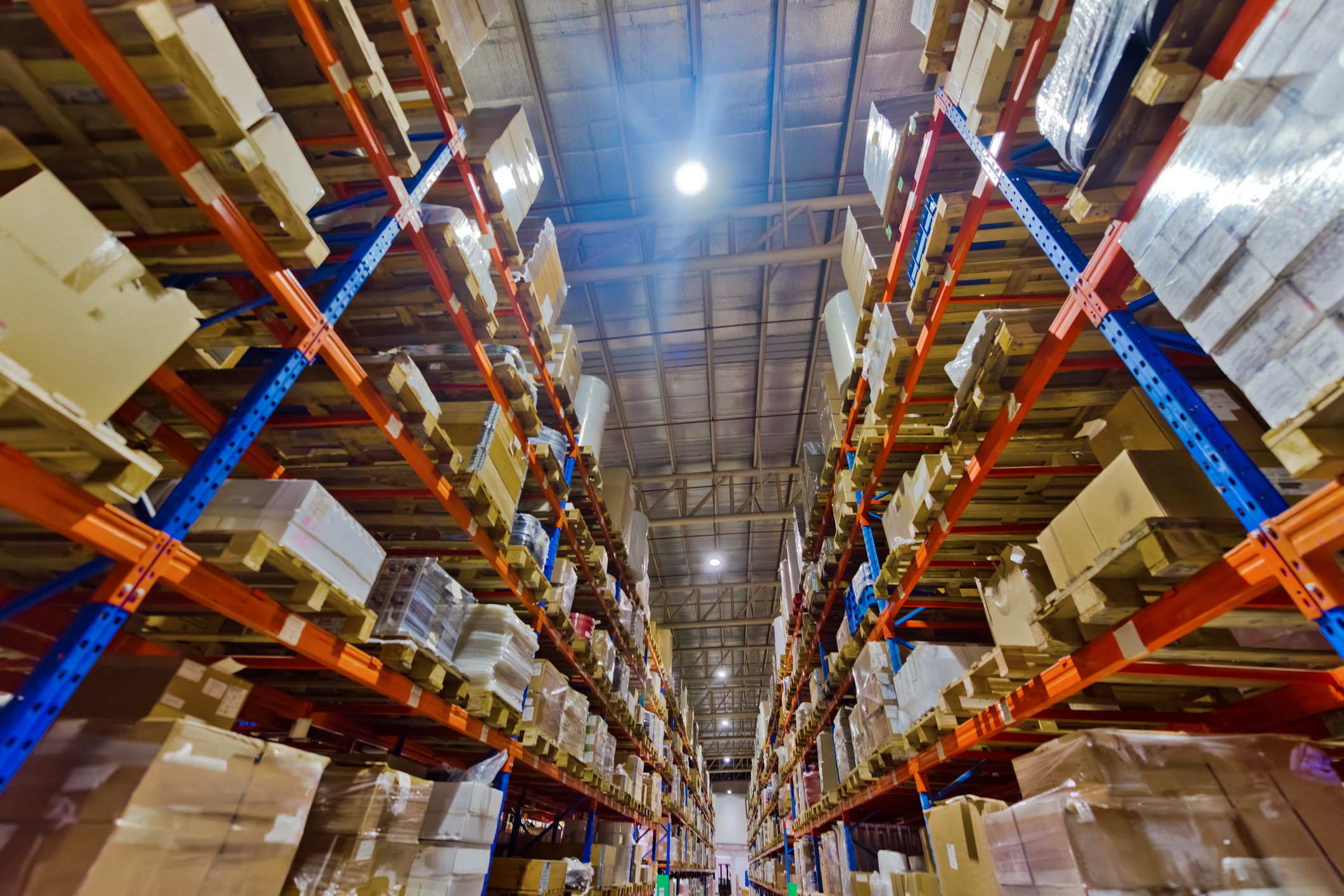
Companies are searching for more warehouse storage as they adopt a ‘just in case’ approach to avoid a repeat of the pandemic driven supply chain crunch. Picture: Getty
And adopting they are. Warehouse storage searches are on the rise, with searches to buy or lease on realcommercial.com.au reaching a record high over the first quarter of 2023.
Meanwhile Prological’s report shows 64% of Australian businesses plan to expand or relocate their warehouse operations in the next two years, with 77% looking to increase their investment in freight and supply chain operations.
While this trend bodes well for commercial real estate, Flaherty cautions that the shift to just-in-case logistics can negatively affect consumers.
“It implies reduced efficiency and higher production prices, which will be passed on.”
Ray White Corporate’s head of research, Vanessa Rader, acknowledges the financial challenges of reshoring and onshoring manufacturing, but notes that warehousing can be a more economically feasible option compared to setting up manufacturing facilities.
“The viability to manufacture goods in Australia will be difficult for some businesses and the overall cost on the consumer. Labour is the major issue here,” she said.
Enter industry 4.0
However, KPMG’s manufacturing lead Tim Plenderleith said the Australian manufacturing industry is experiencing a revival, driven by new technology and automation, which can offset labor costs while enhancing speed and efficiency, which in turn can lower capital inventory.
“Australia today has less unskilled labour, more highly skilled labour and more expensive labour, and this new way of manufacturing suits our emerging industrial needs,” he said.
“It’s less about arms and legs and more about robotics, data, analytics and optimisation, which doesn’t have the same labour requirement. Degree-qualified staff are now the operators.
“Even with Australia’s high cost of capital, high cost of labour and all our supply chain challenges, companies have shown these efficiencies can make it highly competitive and profitable. The car industry simply didn’t transition the way it needed to.”
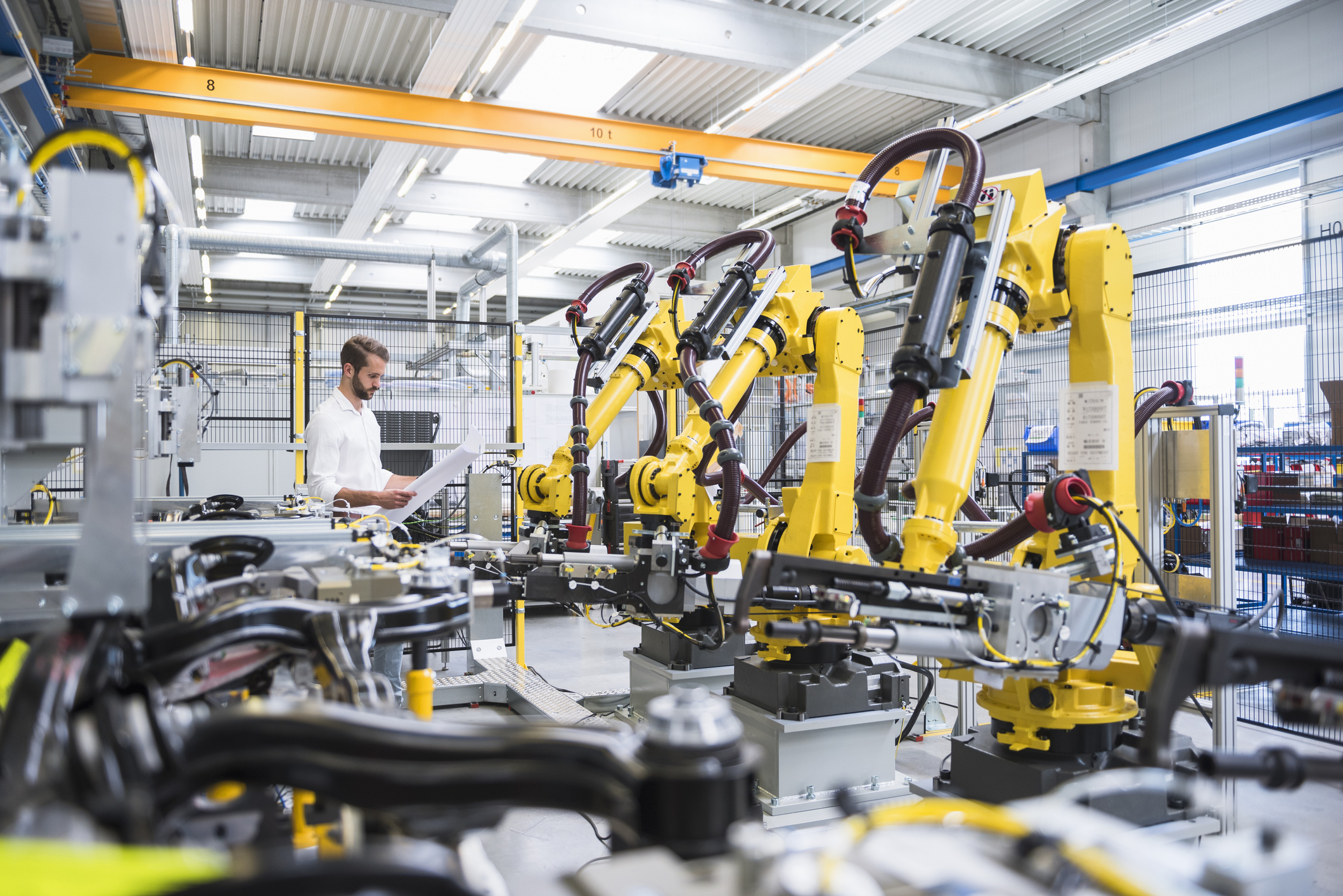
Advances in technology are reducing labour costs in Australian manufacturing. Picture: Getty
Manufacturers can now operate around the clock, thanks to automation, while local production also reduces shipping costs and a company’s environmental footprint, while supporting Australian-made goods.
The benefits of reshoring manufacturing are bolstered by the Albanese Government’s ‘Buy Australia’ plan, which is intended to help create a ‘smart economy’.
Meanwhile, The Australia Institute Centre for Future Work Report in 2020 spoke of the enormous benefits of fostering a competitive advanced manufacturing sector in Australia, given the country’s highly skilled workforce, culture of innovation, modern cities, infrastructure, raw materials and strong research institutions.
Escalating demand for industrial property
Mr Plenderleith says seizing the advantages of domestic manufacturing requires bold reinvestment and strategic partnerships.
“We’re already seeing a lot more integration between businesses and third-party logistics companies. Highly automated warehouses can actually manage inbound and outbound products more efficiently, keep their stock control up to date and drive that speed to market.”
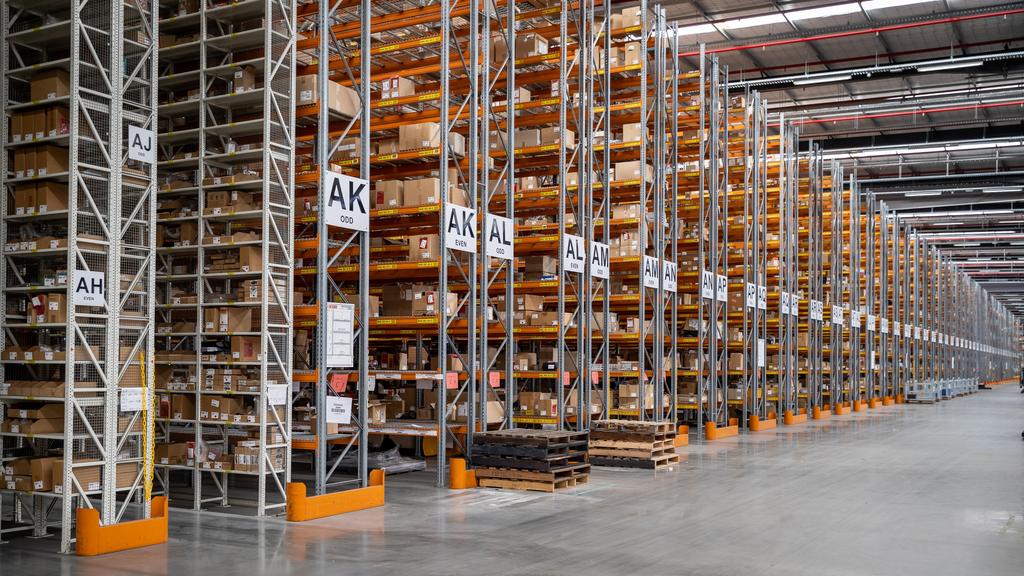
Industrial property values are holding up on the back of surging rents and companies making long-term commitments.
Ms Rader notes that the sustained rise in e-commerce ensures continued high demand for industrial properties.
“The need for logistics, warehousing and storage of goods is not going away, consumption levels remain high and our population is growing, which will increase our need for goods.”
Reshoring or onshoring manufacturing may only boost that demand, she added.
“Given the mismatch in supply and demand, any new source of requirement will pressure rents and values. Markets with a limited land resource in the industrial sector will also push these values up.”