Labour shortage construction sector’s biggest pressure for 2023
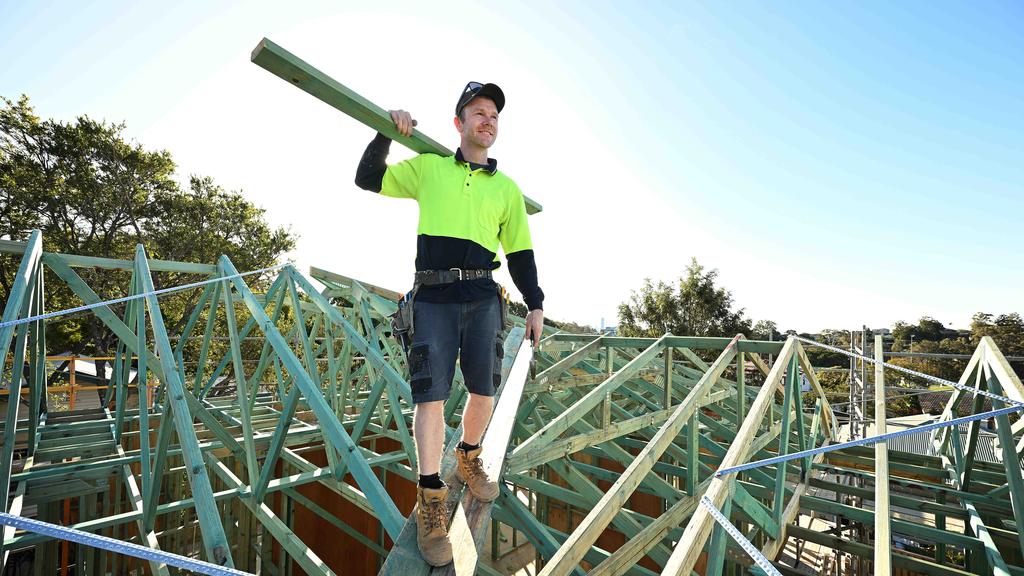
Labor shortages has been described as the biggest issue facing the industry this year. Picture: Lyndon Mechielsen
Labour shortages have been labelled the “single biggest pressure” affecting the construction industry through 2023 as activity begins to slow.
Construction faces a difficult year ahead after rapidly rising interest rates put additional pressure on an industry already facing materials and labour shortages which have claimed a number of big name builders.
Forecasts by Master Builders Australia released this week suggest activity will decline this financial year and next to around $210bn across the industry, with civil construction underpinning the pipeline.
MBA chief executive Denita Wawn said lagging migration and a lack of skilled workers entering the country had meant the broadbased shortage of labour was persisting.
“If you look at the migration numbers at the moment, it’s predominantly students and backpackers,” Ms Wawn said.
“Until such time as the department gets back up to speed on the skilled permanent migration applications … we still think there‘s a good 12 month lag to be impacted by the skills shortage.”
Residential housing is expected to take a hit over the next three financial years after a bumper three years of activity on the back of pandemic stimulus and excess savings. The industry is not expected to get back to building 200,000 homes each year, which is considered necessary to meet population demand, until 2026/27.
Cost pressures on materials have become less pronounced, with MBA chief economist Shane Garrett noting a switch in the products drawing the most costs.
“Labour is probably the single biggest pressure now,” Mr Garrett said.
“The figures show that building materials have slowed down in terms of the rate they’re growing. But, I would caution to say that there’s a bit of a switch going on.”
Costs of steel rose 15.9 per cent last year due to short supply but showed some signs of easing in the December quarter (down 2.1 per cent) as more products came on to the market and shipping costs eased. Electrical equipment also became cheaper (0.3 per cent) last quarter.
Meanwhile, the price of materials like ceramics, cement and concrete have all began to rise, which Mr Garrett said is linked to the gas and heating used through each product’s manufacturing process.
“Obviously, the price of gas going up, it’s only inevitable that the prices of those products go up,” Mr Garrett said. “But, as I say, steel prices are falling and may continue to do so. There’s some signs that some areas of the timber market is experiencing price falls as well structured timber actually dropped in price over the last few months of last year, hopefully that is a trend that will continue.”
Australian Bureau of Statistics data showed the cost of materials to build a house rose 2.2 per cent over the December quarter, to finish last year 14.2 per cent more expensive.
Ms Wawn said that the bulk of fixed price contracts agreed to prior to the pandemic will be completed over the next six months, and some of that pressure off of builders now that projects are moving forward will be priced according to the market.